TM 5-3610-286-20
2-4.
Checking Unpacked Equipment.
a. Inspect the equipment for damage incurred during shipment. If the equipment has been
damaged, report the damage on SF Form 364, Report of Discrepancy (ROD).
b. Check the equipment against the packing slip to see if the shipment is complete. Report all
discrepancies in accordance with the instructions of DA PAM 738-750.
c. Check to see whether the equipment has been modified.
2-5.
Initial Service. The printing press has a protective coating that must be removed.
WARNING
CLEANING SOLVENT. Lithographic solvent is toxic and flammable, Wear
protective goggles and gloves and use only in a well ventilated area. Avoid
contact with skin, eyes, and clothes and dont breathe vapors. Do not use
near open flame or excessive heat. If you become dizzy while using cleaning
solvent, get fresh air immediately and get medical aid. If contact with eyes is
made, wash your eyes with water and get medical aid immediately.
Using a rag dampened with lithographic solvent, wipe down all surfaces until coating is completely
removed. Lightly oil all exposed metal parts.
2-6.
Operational Check. Perform all organizational PMCS as required by Table 2-1. Observe all
warnings and safety precautions. Run the printing press at washup speed to ensure it operates
properly, Check that all safety switches on gates, guards and covers are operating to protect
personnel and to prevent damage to equipment. If problems exist, troubleshoot in accordance with
Table 2-5.
Section Ill. ORGANIZATIONAL PREVENTIVE MAINTENANCE CHECKS
AND SERVICES (PMCS)
Para.
Page
2-7.
General . . . . . . . . . . . . . . . . . . . . . . . . . . . . . . . . . . . . . . . . . . . . . . . . . . . . . . . . . . . . . . . . . . . . . . . . . . . . . . . . . . . . . . . . . . . . . . . . . . . . . . . . . . . . . . . . . . . . . . . . . . . .
2-2
2-8.
Lubrication . . . . . . . . . . . . . . . . . . . . . . . . . . . . . . . . . . . . . . . . . . . . . . . . . . . . . . . . . . . . . . . . . . .. . . . . . . . . . . . . . . . . . 2-3
2-9.
PMCS Procedures . . . . . . . . . . . . . . . . . . . . . . . . . . . . . . . . . . . . . . . . . . . . . . . . . . . . . . . . . . . . . . . . . . . . . . . . . . . . . . . . . . . . . . . . . . . . . . . . . . . . . . . . . .
2-3
2-7.
General. Organizational maintenance level PMCS are done to ensure that the printing press is
in top operating condition. A comprehensive PMCS program reduces equipment downtime and
increasers the operational readiness of the TSS press section.
a. Routine PMCS. For some printing press components, routine PMCS are not listed in the PMCS
table. Routine PMCS that are listed in the PMCS table are there because others have reported unusual
or significant problems with a particular item. Some routine PMCS should include the following:
(1) Check for loose, broken, or missing operating handles, knobs, and ink fountain keys.
(2) Check for loose safety gates, guards and covers.
(3) Check vacuum and compressed air hoses for cracks, sponginess, or evidence of drying
out and brittleness.
2-2
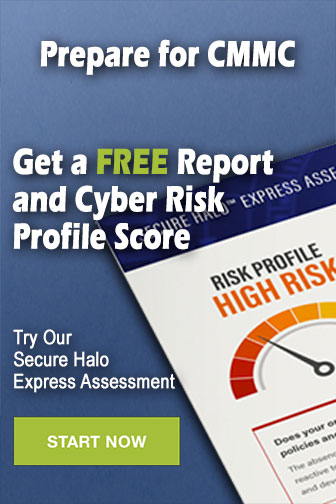