TM 5-3610-286-20
1-11.
Supporting Functions (cont).
c. Sheet Separation. Sheets of paper in piles tend to stick together. Compressed air is blown at
the edge of the paper pile to separate the sheets. This allows atmospheric pressure to be applied
behind each sheet, allowing the lifting suckers to work. Similarly, static electricity build up in the
paper pile will cause paper to stick together. It will also cause the paper to misfeed through the press,
and may sometimes repel ink. A neutralizer bar mounted in the feeder is used to eliminate static
charges from the paper.
d. Sheet Feed. Sheets of paper are lifted to the edge of the feeder table by the suction head.
Moving belts on the table surface pull the paper down across the table when the suction head suckers
release the sheet. The vacuum applied from below through holes in the table, and rotating wheels on
top of the paper sheets, keep the sheets smooth and running straight down to the front lays of the
press. Here, they are alined with the press and ready to be printed. This successive feeding of
individual sheets of paper in a stream is what is referred to when the press is called stream fed.
e. Sheet Transport. Since thin sheets of paper cannot be pushed without crumpling, they are
always pulled through the press. Mechanical grippers grasp the leading edge of each sheet of paper
as it reaches a particular position in the press. They then release the paper when it is time for it to
leave that position. Thus, the sheet of paper is handed off from position to position. Paper presented
to the press by the feeder table is grasped by the ranger drum and moved to where it can be grasped by
the impression cylinder. The ranger drum grippers release, the impression cylinder grippers grasp,
and the paper wraps around the impression cylinder to be printed. After printing, the impression
cylinder grippers release the paper. The edge of the paper, guided and supported by the transport
(skeleton) cylinder, is grasped by the delivery end grippers and pulled off of the impression cylinder.
The delivery end grippers release when the printed sheet is over the suction slowdown assembly. This
assembly applies a vacuum to the sheet, through rotating suction wheels, slowing down the released
sheet so that it does not overshoot the delivery end paper pile. Finally, a blast of compressed air
directs the paper downward onto the delivery end paper pile.
1-12.
Control and Monitoring. In addition to mechanical controls for operating and adjusting press
components, and electrical controls for operating the press and the feeder, an electronic control box
and related light sensors are built in to the press to monitor operation. The press will not goon im-
pression if no paper has reached the front lays or if the press has not reached the preset operating
speed. The press will also not go on impression if a misalined sheet of paper enters the press.
1-13.
Lubrication. In general, most moving components of the press that are lubricated by oil are
serviced by a central lubrication distribution system. Oil stored in a reservoir is drawn out by a sub-
merged pump when a manually actuated valve is operated by the press operator as directed by oper-
ators PMCS. This oil is distributed by pressure, generated by valve operation, to various lubrication
heads. These are located between the press main guard (D/S) and the D/S side plate, between the
upper guard (O/S) and the O/S side plate, and over the sprocket drives in the feeder. These heads
have a number of metered valves that dispense oil at a predetermined flow rate to fittings on various
rotating components. In addition, some valves feed open-end tubes from which oil is allowed to drip
onto moving surfaces, such as cams, for lubrication. Some components, such as the main motor and
the compressor, are not part of the system and must be lubricated separately. Additionally, many of
the press rollers have bearings that must be lubricated by grease. These are equipped with grease
fittings for manual lubrication.
1-16
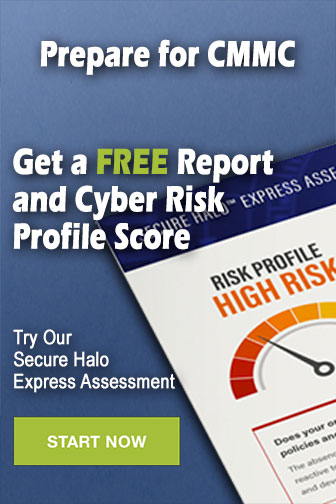