TM 5-3610-286-20
Lithography is based on the principle that grease and water do not mix, but actually repel each other.
Water is applied to the printing plate to moisten it. Then, a greasy printing ink is applied to the plate.
The matter to be printed accepts the ink, while the blank surface of the plate which is wet rejects the
ink. Then, the inked matter to be printed can be transferred to paper.
b. Photolithography. Printing plates can be made of many types of materials, usually stone or
metal. Metal plates have the advantage that they can be made thin enough to wrap around a cylinder in
a rotary type printing press. This makes high speed printing possible. The TSS printing press output is
variable up to 6,000 impression per hour. Metal printing plates are made by a photographic process.
The plate, usually made of zinc or aluminum, is given a sensitive coating. The plate is exposed to light
through a negative of the matter to be printed and then developed, washed and etched. The etching
process creates the rough surface that holds the greasy ink, while the smooth, unetched surface only
holds water.
c. Offset Printing. Generally, the matter to be printed (the image on the printing plate) is not
transferred directly onto the paper. It is first transferred to an intermediate, rubber cylinder (the
blanket cylinder) which then transfers (offsets) the image to the paper. Because of the flexibility of the
rubber cylinder, the image can be transferred to paper of many different thickness, to cardboard, and
to other materials. The offset printing press normally contains three rotating cylinders. The plate
cylinder carries the metal printing plate which is wrapped around it and clamped in place. The blanket
cylinder carries the rubber blanket which is wrapped around the cylinder and clamped in place. The
impression cylinder presses the paper against the blanket cylinder. Moistening rollers, which apply a
film of water to the plate, and inking rollers, which apply ink to the plate, comprise the remaining
components used in the offset printing process.
1-11.
Supporting Functions. The primary functions that support offset printing are concerned with
moving blank paper into and through the press and delivering printed paper out of the press. Elec-
trical, electronic, and mechanical devices are used to control and monitor these functions. Safety
devices are provided to protect the operator.
a. Paper Lifting. Large quantities, or piles, of paper are carried on wooden pallets. The entire
pallet is lifted in the feeder by means of a pile lift motor and a chain and sprocket arrangement. Lifting
is timed so that the top sheet of the pile is always high enough to be picked up by the suction head. Pile
lifting stops when the last sheet is fed into the press. A similar arrangement of pile lift motor and chain
and sprocket drive is located under the delivery end of the press. Printed paper is transported to the
top of the pile. The pile pallet is lowered so there is room for each printed sheet to drop onto the top of
the pile. The delivery pile motor stops when the pile pallet is fully loaded, usually when the pallet
reaches the floor. Limit switches determine the upper and lower limits of lift of the pallets. The feeder
and delivery pile motors are interlocked so that if one stops, the other also stops, preventing paper
pileup. The TSS printing press has a second feeder pile lift motor and chain and sprocket drive to
allow continuous feed operation. In this mode, a continuous feed rake is inserted into the delivery end
of the press to catch printed pages instead of the delivery pallet. A limit switch, operated by inserting
the rake, keeps the delivery pile motor shut off in continuous feed operation.
b. Sheet Lifting. Individual sheets of paper are flimsy and easily crumpled, yet difficult to pick up
Sheet lifting is accomplished by means of suction. A vacuum is created in a pump and directed to a
sucker head which is placed against the paper. Atmospheric pressure behind the paper forces the
paper against the sucker head. When the head is moved, the paper moves with it. When the sucker
has brought the sheet of paper to the desired position, the vacuum is cut off, releasing the paper.
1-15
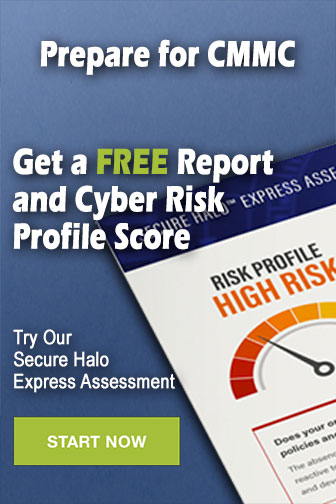