TM 5-6675-319-14
(b) When the negative (-) switch on the TILT assembly is depressed a
low is felt on pins 5 and 9 0f IC1.
Q2s conduction causes relay K2 to energize.
The contacts of K2 apply L1 (115 V ac) to one side of relay K4, energizing it. The
dc to dc converter output is applied to TB A1 and A2. The direction of rotation is
controlled by relay K4.
K4 feeds the armature power supply from TB + (positive)
through its lower contacts to TB2 A2.
The dc output from pins A1 and A2 on TB2 is
applied to chassis TB1 pin 8 and 9 then to the dc motor armature.
( c ) T h e m o t o r w i l l t u r n l e f t , d e c r e a s i n g t i l t u n t i l t h e - s w i t c h is
r e l e a s e d o r t h e f r o n t t i l t l i m i t s w i t c h o p e n s. When the - switch is released, pins 5
and 9 of IC1 output goes high.
This cuts off Q2 and de-energizes relays K2 and K4.
( 5 ) T i l t m o t o r d r i v e d y n a m i c b r a k i n g c i r c u i t .
(a) Relays K1 thru K4 are de-energized. The armature power supply
output is removed from the armature.
The armature power supply is fed through the
de-energized contacts of K2 and K1 to current limiting resistor R15. The dc to dc
converters output is fed through the de-energized contacts of K3 and K4 to dynamic
braking resistor R16.
The output of motor control bridge rectifier remains
connected to pin F1 to the field winding via chassis TB pin 14, field weakening
resistor (F resistor), chassis TB1 pin 11 and pin F2. The interaction of the
rapidly weakening armature field and the field winding magnetic fields attempts to
r e v e r s e t h e m o t o r s d i r e c t i o n r a p i d l y .
The effect is to dynamically brake the motor
to a complete stop.
Since the ac variations are decreasing in amplitude, this
decrease is felt on motor control TB pin A2 and is fed to reversing contactor TB3
pin 7 through relay K1 and K2 and out TB3 pin 6 to motor control TB pin P2. This
reverse biases Q2 which holds Q1 and the SCR off, ensuring that the motor cannot
increase speed during braking operations.
If one or more of the limit switches
opens, the sequence of events just described occurs.
(b) Tilt drive motor SLOW and SLEW speed operations are identical to
mag drive motor description.
T i l t d r i v e m o t o r c o n t r o l a d j u s t m e n t s a r e i d e n t i c a l t o
the mag drive motor description.
(6) Magnification dynamic drive braking. Relays K1 through K4 are de-
energized.
The armature power supply output is removed from the armature. The
armature power supply is fed through the de-energized contacts of K2 and K1 to
c u r r e n t l i m i t i n g r e s i s t o r R 1 5 .
The dc to dc converter output is fed through the de-
energized contacts of K3 and K4 to dynamic braking resistor R16. The output of the
motor control bridge rectifier consisting of diodes K1 thru K4 and transient supres-
sor SP1 is connected to pin F1 to field winding via chassis TB1 pin 14, field
weakening resistor (F resistor), chassis TB1 pin 11 and pin F2. The interaction of
the rapidly weakening armature field and the field winding magnetic field attempts
t o r e v e r s e t h e m o t o r s d i r e c t i o n r a p i d l y.
The effect is to dynamically brake the
motor to a complete stop.
Since the ac variations are decreasing in amplitude, this
decrease is felt on motor control TB pin A2 and is fed to reversing contactor TB3
pin 7 through relays K2 and K1 and out TB pin 6 to motor control TB pin P2. This
reverse biases Q2, which holds Q1 and SCR off, ensuring that the motor does not
attempt to increase speed during braking operations.
If one or more of the limit
switches opens, the operation identical to the one just described occurs.
7-17
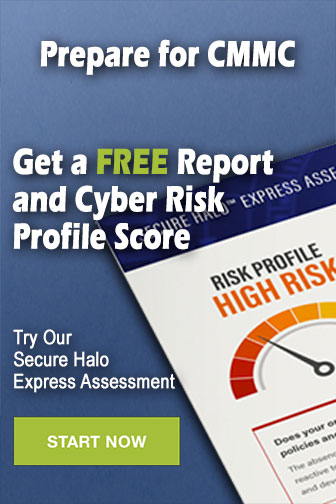