Change 3
TM 5-6675-302-14&P
equipment if operation were to continue. All defi-
ciencies and shortcomings shall be recorded
together with the corrective action taken on DA
Form 2404, Equipment Inspection and Mainte-
nance Worksheet, at the earliest opportunity.
When performing your Before Operation (B) and
During Operation (D) PMCS, always keep in mind
the CAUTIONS and WARNINGS. After opera-
tion, be sure to perform your (A) PMCS. If your
equipment fails to operate, troubleshoot with pro-
per equipment. Report any deficiencies using the
proper forms, see TM 38-750.
4-5. Preventive Maintenance Checks and Ser-
vices. Refer to Table 4-2 for Preventive Mainte-
nance Checks and Services.
a. Item Number Column. Checks and services
are numbered in chronological order regardless of
interval. This column will be used as a source of
item numbers for the TM item number column on
DA Form 2404 in recording results of PMCS.
b. D e l e t e d .
Table 4-2. Organizational Preventive Maintenance Check and Services
Legend
W--Weekly
Q--Quarterly
A--Annually
H--Hours
M--Monthly
S--Semiannually
B--Biennially
MI--Miles
Interval
Item
Item
For Readiness Reporting,
No.
To Be
Procedure
Equipment Is Not Ready/
W M Q
S
A
B
H
MI
Inspected
Available If
1
l
Accessory case
Check for serviceability and
presence of components.
2
l
Battery box
Check for serviceability and
presence of components.
Check batteries and wiring
Faulty batteries
for serviceability. Check
rheostat for tight and clean
connections and proper
operation.
3
l
Hand lamp
Check for serviceability and
Defective lamp
p r o p e r o p e r a t i o n .
4
l
Tripod
Check for serviceability.
5
l
All components
Check for proper function,
alignment, adjustment, and
calibration.
6
l
Surveying set
Make all necessary ad-
justment and operational
tests. Lubricate target
set.
4-2
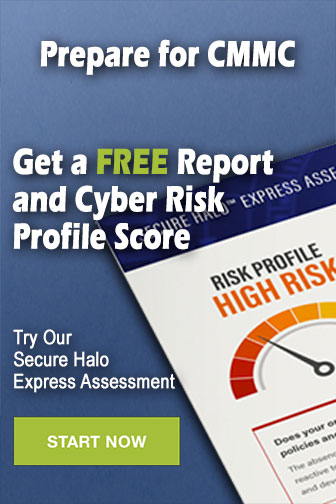