TM 5-6675-319-14
(2) Primary power is applied to tilt and mag block pins 1 and 2, reversing
contactor modules TB2 pins L1 and L2 and transformer T1.
(3) Hal f wave rectification and filtering is accomplished by diode D3 and
capacitor C8.
This output is used by the dc to dc converter consisting of R10, R13,
IC3, Q3, R12, R14, C7 and bridge rectifier D6 through D9. A full wave rectifier
consisting of diodes 04 and D5, filters C9, C10, C11 provides an unregulated output
to regulator IC2.
IC2 regulates the output to 5 V dc and is nonadjustable.
(4) Primary power is applied to tilt and mag chassis terminal blocks pins
1 and 2, motor control terminal blocks pins L1 and L2, 3 amp fuse FU1, a filter
network consisting of L1 and C6 and the bridge rectifier.
T h e b r i d g e r e c t i f i er
consists of diodes D1 thru D4 and transient suppressor SP1. The output of the bridge
rectifier provides dc voltages for the field winding and armature power supply. The
field winding power supply consists of bridge rectifier, field weakening resistor (F.
Res.), and the field winding.
The field winding power supply provides 100 V dc at
200 mA. The armature power supply consists of voltage divider network consisting of
R1, R2, the motor armature, P3, P5, SLOW or SLEW speed potentiometer R12, P4 and
R11. The dc motor speed and armature current is regulated by the SLEW or SLOW speed
wiper arm Q2, Q1, T1 and SCR.
Q3 provides a referenced level when the motor is
stopped.
The armature power supply provides an output of 125 V dc at 700 mA when
the motor is not rotating.
A rotating armature voltage can be from 0-115 V dc. The
motor control is protected by a three ampere fast blow fuse.
7-25
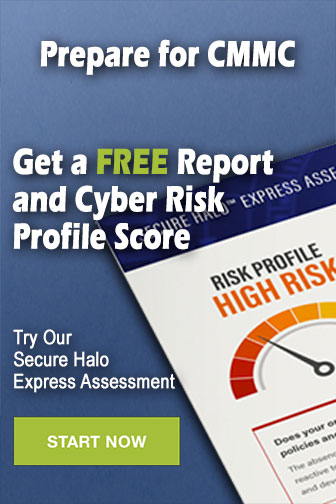