ARMY TM 5-6675-238-14
MARINE CORPS TM 08839A-14/1
(4) SPU basic control logic test. Before the vari-
ous functional segments in the SPU can be self-tested, it
is necessary to test the basic logic in the SPU that
controls the serial data bus circuitry. This basic logic
includes registers and steering logic for self-test tape
data. It also includes address decode logic and parity
check logic which is common to all of the SPU func-
tional segments. By reading known address and parity
data from the self-test tape and comparing that decoded
parity and address to the expected parity and address,
the SPU basic control logic is determined to be operat-
ing properly, or else a failure has occurred, If the SPU
basic control logic is operating properly, the self-test
tape is advanced to the first functional segment test. If a
failure occurs in the SPU basic control logic, a special
code is displayed on the FAILURE/ACTION indicator.
closer self-test is functionally illustrated in figure FO-11
and is contained on logic no. 3 electronic component
assembly A3. The tape reader supplies data that is used
for all control functions. The 2.4-kHz clock is gated on
or off by BITE circuitry control. The differential
line drivers are first tested statically with the clock off.
Next the clock is gated on and the differential
line driver outputs are checked. The clock pulses should
appear on all output lines, The clock circuitry is
checked separately. The clock is tested for both correct
amplitude and correct frequency.
(6) Serial dirts bus loop closer self-test. The serial
data bus loop closer self-test is functionally illustrated
in figure FO-12 and is contained on logic no. 1 elec-
tronic component assembly Al and logic no. 3 elec-
tronic component assembly A3. The tape reader sends
the specific address to activate the serial data bus loop-
around circuitry. The self-test tape data is used to
duplicate the normal computer serial data bus data and
control functions. BITE circuitry for the serial data bus
loop-around circuitry are the self-test tape to serial data
bus conversion logic, input data parity generation,
check and store, and compare logic. The address word
from the self-test tape is stored and decoded, then
parity is checked. If parity is correct, a data envelope
signal and a clock signal are received from the self-test
tape. The data envelope signal causes the address word
to be shifted out of the storage register. The address
word is inverted as it shifts out and back in simulta-
neously. Parity is checked against the expected parity of
the inverted address. If the parity of the output data
from the address/data line receiver is opposite to the
parity of the original address word, the serial data bus
loop-around circuitry is considered good. However, if
the serial data bus fails to perform certain tests, then
the time-out counter is not reset causing a serial data
bus failure indication. BITE circuitry then goes on to
the next functional test.
(7) Teletypewriter control logic self-test. The tele-
typewriter control logic self-test is functionally illus-
trated in figure FO-13 and is contained on logic no. 1
electronic component assembly Al. BITE circuitry for
the teletypewriter circuitry self-test are the self-test
tape to DMA control and compare logic. The tape
reader sends the specific address that activates the
teletypewriter circuitry in the SPU. A universal asyn-
chronous receiver/transmitter (UART) module is used
for control of the teletypewriter. The UART normally
communicates with the computer via the computer
data bus. However, for SPU built-in-test, the DMA data
lines that are common to the computer data bus are to
communicate with the UART. After the teletypewriter
circuitry has been activated via an address word from
the self-test tape, a data word from the tape is loaded
into the UART send register. Next, a command word
from the tape is loaded into the UART control register.
This control word initiates the UART send/receive
cycle. On the send cycle the data in the send register is
converted to serial form and given start code, stop
code, and timing characteristics in accordance with the
type of teletypewriter involved. For the built-in test,
the serial data to the teletypewriter is wrapped back as
an input to the serial data from the teletypewriter.
Hence, a total SPU teletypewriter circuitry check is
made without having to connect the teletypewriter to
the SPU. The SPU teletypewriter self-test compares the
parallel data from the UART receive register to the
parallel data from the send register. If the comparison
checks good, the SPU teletypewriter circuitry is consid-
ered good and the tape reader is advanced to the next
SPU self-test. If the test is not successful, the FAIL-
URWACTION indicator reads out the fault and the
tape reader is halted. If the test is successful, the BITE
circuitry will instruct the operator to hook up the
teletypewriter. Echo checking of any character entered
from the keyboard can now be made ensuring that the
teletypewriter and the SPU current loops are good. If
this echo-check mode is good, the next BITE test is
started by pressing and repressing the SPU SELF TEST
switch.
(8) Digital/resolver
and digital/synchro loop
closer self-test. The digital/resolver and digital/synchro
loop closer self-test is functionally illustrated in figure
FO-14 and is contained on logic no. 1 electronic com-
ponent assembly Al. BITE circuitry for the digital/
resolver and digital/synchro loop closer self-test are the
self-test tape to serial data bus conversion logic, refer-
ence generator, amplifier and phase shift test circuit,
precision amplifier-ratio test circuit, and overall test
good or no good circuit. The tape reader sends a
specific address to activate the digital/resolver and
digital/synchro loop closer circuit. Then the tape
reader sends the specific 14-bit angle which is used for
the self-test. Since the self-test tape data is made to
look like the computer serial data bus, the self-test
exercises the loop closer circuitry in the same way as it
6-11
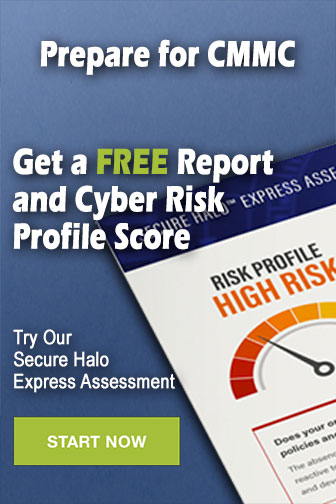