TM 5-3610-286-20
2-96.
Adjustment of Timing Settings (cont).
(2) Degree Settings for printing unit. Turn the press by hand and observe that the machine
operations listed in table 2-6 occur at the degree setting indicated on the graduated disc opposite the
mark on the oil catcher strap. If the machine operations occur at the correct position (degree
setting), the timing of press operations is correct. If not, adjust as described in the appropriate
maintenance paragraph.
Table 2-6. Degree Settings for Printing Unit.
Setting (Degrees)
Operation
0°
Zero position: impression cylinder mark D meets edge
of slide gauge
49° (approx.)
Delivery sheet joggers start moving inwards
70°30
Rubber blanket cylinder is in print begin position rela-
tive to impression cylinder (G mark on impression
cylinder)
176°
Delivery grippers closing (A mark on impression cylinder)
177°
Impression cylinder grippers opening
256°
Impression cylinder grippers closing (V mark on
impression cylinder)
257°
Ranger drum grippers opening
290°
Inking vibrator rollers touching ink distributor cylinder
NOTE
Check that grippers are closed by insertion onion skin sheet of paper as grip-
pers are closing. When correctly closed, sheet may be pulled out with slight
drag.
(3) Degree settings for feeder unit. Due to gear backlash, the O position of the press is not
used for paper feed operations timing measurements.
(a) Before taking readings for adjustments performed on the side lays, front lays, and
feeder, reset the graduated disc as follows:
1 Set ranger drum gripper bar to paper.
2 Turn press by hand until the transfer position from the feed table to the ranger drum has
been reached.
3 Check carefully with a small 90 degree square (figure 2-282). The gripper bar of the
ranger drum must form a 90 degree angle with the feed table.
2-550
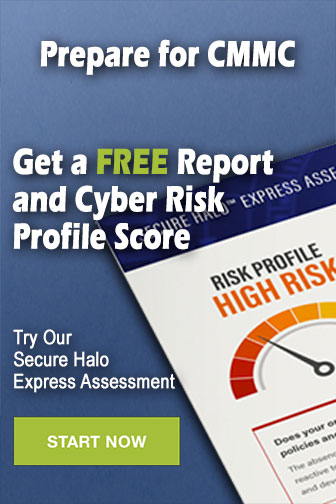