TM 5-6675-315-14
Section IV ORGANIZATIONAL MAINTENANCE
4-11. LUBRICATION INSTRUCTIONS. This equipment does not require lubrication.
4-12. REPAIR PARTS; SPECIAL TOOLS; TEST, MEASUREMENT AND DIAGNOSTIC EQUIPMENT; AND
SUPPORT EQUIPMENT. These items are not required at the organizational level.
4-13. SERVICE UPON RECEIPT.
4-13.1 Checking Unpacked Equipment.
a.
Inspect the equipment for damage incurred during shipment. If the equipment has been damaged, report the
damage on DD Form 6, Packing Improvement Report.
b.
Check the equipment against the packing list to see if the shipment is complete. Report all discrepancies in
accordance with the instructions of DA Pam 738-750.
c.
Check to see whether the equipment has been modified.
4-14. ORGANIZATIONAL PREVENTIVE MAINTENANCE CHECKS AND SERVICES. There are no organizational
PMCS procedures assigned for this equipment.
4-15. ORGANIZATIONAL TROUBLESHOOTING. If the vacuum cleaner does not power up when turned on, verify that
120 V ac is present at the receptacle. If voltage is not present, plug equipment into receptacle with power available and
proceed with equipment troubleshooting. Perform no-power procedures for dead receptacle (Table 1-4). If voltage is
present, replace vacuum cleaner.
4-16. MAINTENANCE PROCEDURES. There are no organizational maintenance procedures assigned for this
equipment.
4-17. PREPARATION FOR STORAGE AND SHIPMENT. Contact your battalion for packing and shipping instructions.
Section V DIRECT/GENERAL SUPPORT MAINTENANCE
There are no direct/general support maintenance procedures assigned for this equipment.
4-9 (4-10 blank)
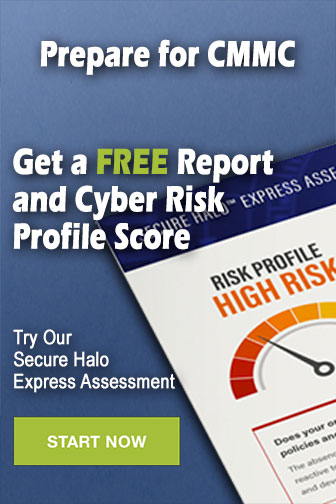