TM 5-6675-325-14
Section IV ORGANIZATIONAL MAINTENANCE
8-11. LUBRICATION INSTRUCTIONS.
This equipment does not require lubrication.
8-12. REPAIR PARTS, SPECIAL TOOLS; TEST, MEASUREMENT,
MENT (TMDE); AND SUPPORT EQUIPMENT.
AND DIAGNOSTIC EQUIP-
8-12.1
Common Tools and Equipment. For authorized common tools and equipment,
refer to the Modified Table of Organization and Equipment (MTOE) applicable to your
unit.
8-12.2 Special Tools: Test. Measurement. and Diagnostic Equipment: and Support
Equipment.
Special Tools, TMDE, and Support Equipment is listed in the applicable
repair parts and special tools list and in Appendix B of this manual.
8-12.3 Repair Parts.
Repair parts are listed and illustrated in the Repair Parts
and Special Tools List, TM 5-6675-325-24P covering organizational maintenance for
this equipment.
8-13. SERVICE UPON RECEIPT.
8-13.1
Checking Unpacked Equipment.
Inspect the equipment for damage incurred during shipment. If the equipment
has been damaged, report the damage on DD Form 6, Packing Improvement Report.
a .
b. Check the equipment against the packing list to see if the shipment is
complete. Report all discrepancies in accordance with the instructions of DA Pam
738-750.
c.
Check to see whether the equipment has been modified.
8-14. ORGANIZATIONAL PREVENTIVE MAINTENANCE CHECKS AND SERVICES. There are
no organizational PMCS procedures assigned for this equipment.
8-15. ORGANIZATIONAL TROUBLESHOOTING PROCEDURES. There are no organizational
troubleshooting procedures assigned for this equipment.
8-16. MAINTENANCE PROCEDURES.
This section contains instructions covering organizational maintenance
fuctions for the furniture and cabinets.
Personnel required are listed only if the
task
a .
b.
sure
requires more than one.
After completing each maintenance procedure, perform operational check to be
that equipment is properly functioning.
8-5
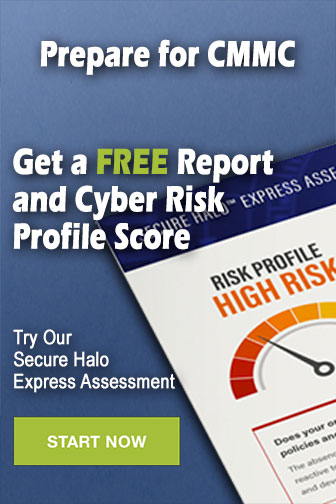